Integrating Software into Industrial Control Panel Design: The Latest Advancements
December 10, 2024
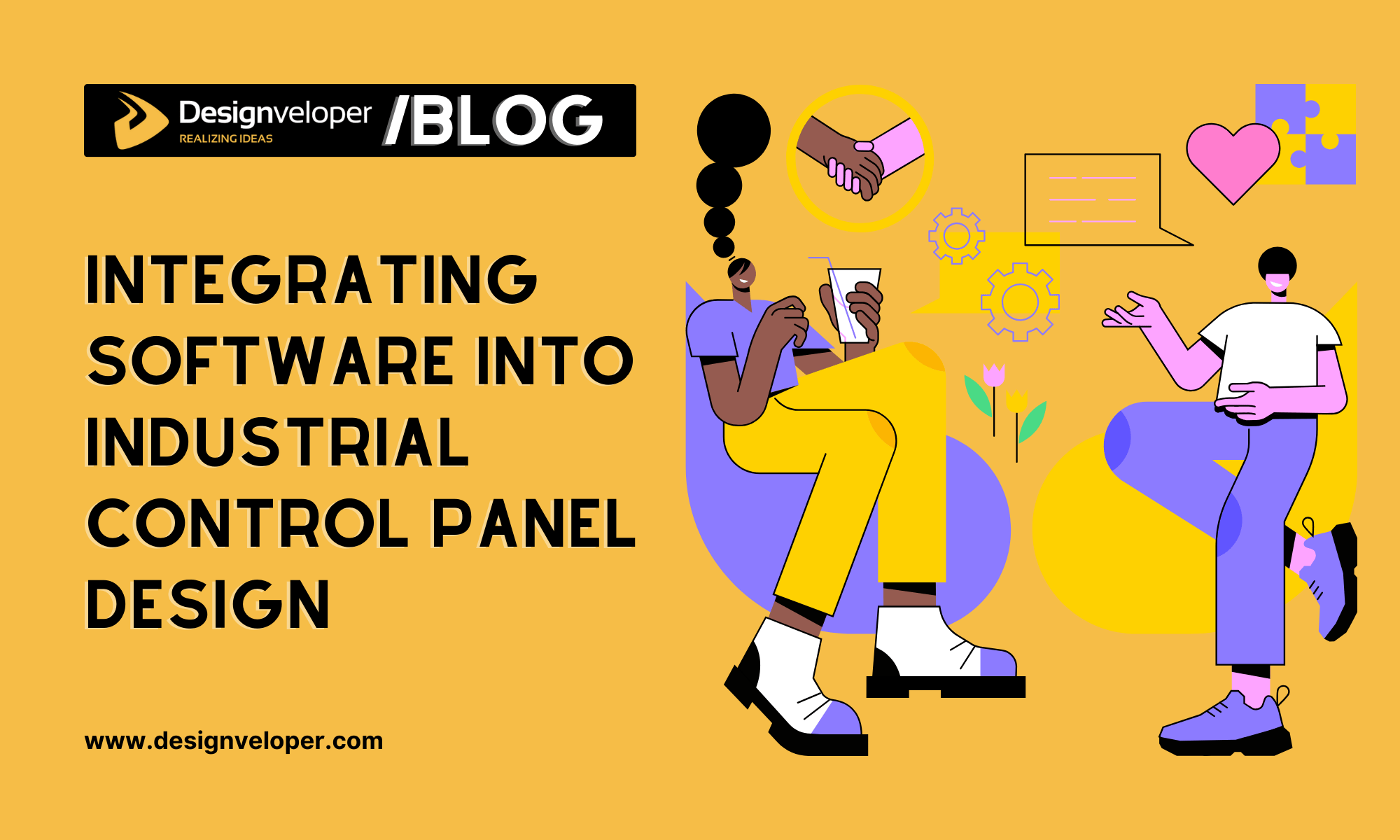
Industrial control panels are essential components in manufacturing and production environments. They serve as the central hub for managing machinery, processes, and operations. Over time, the role of control panels has evolved with the incorporation of advanced software technologies. This integration aims to enhance operational efficiency, reduce downtime, and improve overall control system performance.
With constant advancements in technology, software integration has become a critical factor in modern control panel design. Understanding the latest developments and their applications can help businesses remain competitive in a rapidly changing landscape.
The Role of Software in Modern Control Panel Design
Software has shifted from being a supplementary tool to a core element in control panel design. It provides the ability to monitor, control, and analyze processes with greater precision. The integration of software allows for more effective system management, contributing to improved productivity and operational accuracy.
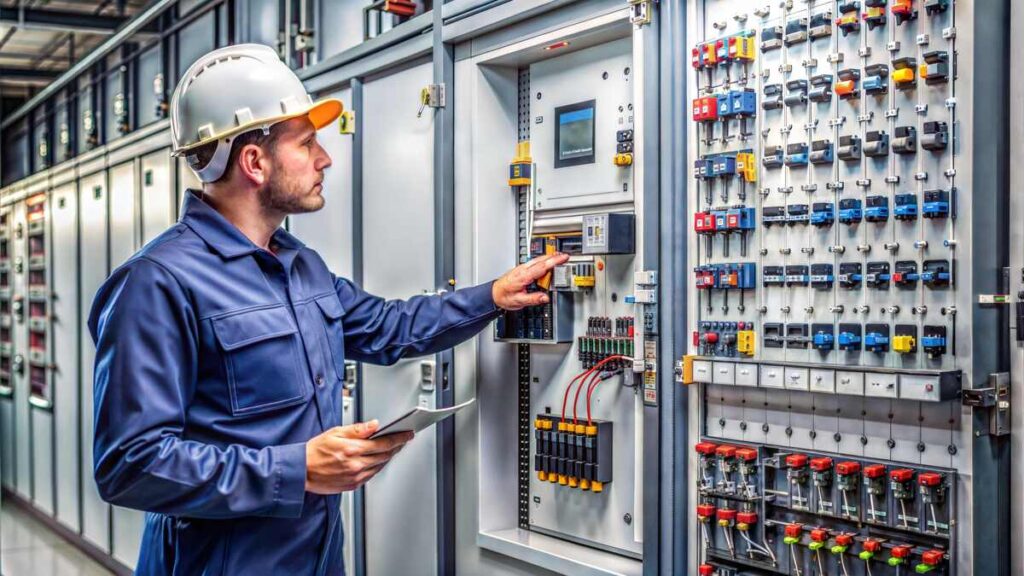
Real-time monitoring enables operators to track performance metrics instantly, making it possible to address potential problems before they escalate. This proactive approach minimizes downtime and enhances reliability. Additionally, software tools offer detailed diagnostics, allowing technicians to pinpoint faults efficiently and reduce repair times.
Enhanced automation is another significant benefit. With tools like programmable logic controllers (PLCs) and human-machine interfaces (HMIs), routine tasks can be automated, ensuring consistency and precision. This capability frees up human resources for more complex tasks and reduces the likelihood of human error.
Advancements in Software Integration
The latest advancements in software for industrial control panels address several key areas, including connectivity, customization, and scalability. Below are some of the most notable developments:
Industrial Internet of Things (IIoT) Integration
The IIoT has revolutionized how industrial systems communicate and operate. By connecting devices through a network, the software can collect and analyze data in real time. This integration offers benefits such as predictive maintenance, which helps businesses avoid costly breakdowns by addressing issues before they occur.
Process optimization is another advantage of IIoT integration. By analyzing data from interconnected devices, businesses can identify inefficiencies and implement corrective measures. For example, sensors in a manufacturing line can monitor equipment performance and alert operators about necessary adjustments, ensuring smooth operations.
Cloud-Based Solutions
Cloud technology is increasingly used for data storage and remote monitoring. Software integrated with cloud platforms allows businesses to access system data from any location. This capability is particularly valuable for multi-site operations, where centralized oversight is crucial.
By leveraging cloud solutions, companies can enhance collaboration among teams located in different regions. For example, a manufacturing company can consolidate data from multiple facilities, enabling management to make informed decisions using a unified dashboard. This approach improves efficiency and ensures data consistency across locations.
Machine Learning and Artificial Intelligence (AI)
Machine learning algorithms are being embedded into control panel software to enable systems to learn from operational data. These tools excel at detecting patterns and forecasting potential issues, allowing for preemptive measures.
For example, an AI-powered control panel can analyze energy consumption patterns and recommend optimizations to reduce costs. Additionally, machine learning tools help improve control system reliability by identifying anomalies that may indicate equipment failure, preventing costly disruptions.
User-Friendly Interfaces
Modern software prioritizes ease of use through intuitive interfaces. Touchscreen HMIs, for example, allow operators to interact with control systems seamlessly. These interfaces are designed to provide actionable insights without overwhelming users with unnecessary information.
Customizable dashboards further enhance user experience by enabling operators to focus on metrics most relevant to their tasks. This flexibility ensures that operators can respond to changing conditions efficiently, improving overall productivity.
Edge Computing
Edge computing involves processing data locally rather than relying solely on cloud-based systems. This approach minimizes latency and ensures uninterrupted operations even during connectivity issues. For example, a control panel equipped with edge computing can manage essential processes independently, maintaining system stability.
In industries where split-second decisions are critical, edge computing offers significant advantages. It enables real-time data processing, ensuring that control systems respond to operational changes immediately, enhancing efficiency and safety.
By embracing these advancements, businesses can enhance their operational capabilities and remain competitive in an ever-evolving industrial landscape.
Benefits of Software Integration in Control Panel Design
The integration of software into industrial control panels brings numerous advantages that extend beyond traditional hardware capabilities. These benefits include:
Increased Efficiency
Automation and advanced monitoring tools reduce manual intervention, allowing systems to run more efficiently. For instance, conveyor systems equipped with integrated software can automatically adjust speeds based on production demands. This capability ensures that resources are utilized optimally, reducing waste and enhancing throughput.
Additionally, integrated software allows for better coordination among different components of a production line. By synchronizing operations, businesses can achieve smoother workflows and minimize delays caused by miscommunication or system inefficiencies.
Enhanced Safety
Software can integrate safety features such as emergency stop mechanisms and real-time alerts. By analyzing data, it can also predict hazardous conditions and take preventive measures. A food processing plant, for instance, can use software to monitor temperature and ensure compliance with safety standards.
Advanced safety features also include automated responses to potential risks. For example, software can shut down machinery when unsafe conditions are detected, protecting workers and minimizing the likelihood of accidents.
Cost Savings
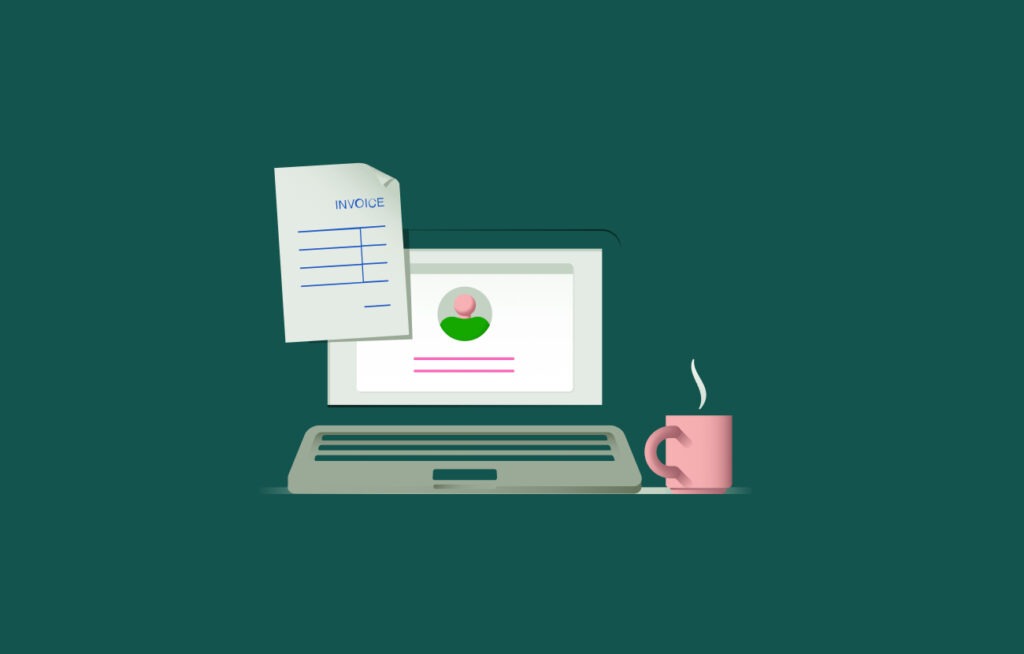
Predictive maintenance, facilitated by integrated software, minimizes unexpected downtime and reduces repair costs. By identifying potential failures before they occur, businesses can avoid expensive disruptions and extend the lifespan of their equipment.
Energy management tools also contribute to cost savings. By monitoring and optimizing energy use, software can help industries reduce utility expenses, contributing to both financial and environmental benefits.
Scalability
As businesses grow, software solutions can be updated or expanded to meet increasing demands. This scalability ensures that control systems remain relevant and effective over time. For example, manufacturers can add new functionalities to their software as production requirements evolve, avoiding the need for costly hardware upgrades.
Scalability also supports innovation. With flexible software platforms, businesses can adopt new technologies and processes without overhauling their existing systems, ensuring long-term competitiveness.
By incorporating these benefits, industries can optimize their operations and achieve sustainable growth in competitive markets.
Overcoming Challenges in Software Integration
While the benefits are significant, integrating software into control panel design comes with challenges. Addressing these issues is crucial for successful implementation.
Compatibility
Ensuring that new software is compatible with existing hardware can be a complex process. Manufacturers must choose solutions that support standard protocols such as Modbus, Ethernet/IP, or OPC UA. Compatibility issues can lead to inefficiencies and delays during the integration process.
To overcome these challenges, businesses should collaborate with experienced vendors and engineers. By selecting software solutions that align with their specific needs, they can ensure a smoother implementation and maximize the benefits of integration.
Cybersecurity
With increased connectivity comes a greater risk of cyberattacks. Control panel software must include robust security measures, such as encryption and user authentication, to protect sensitive data. Cybersecurity is especially critical in industries handling confidential information or operating critical infrastructure.
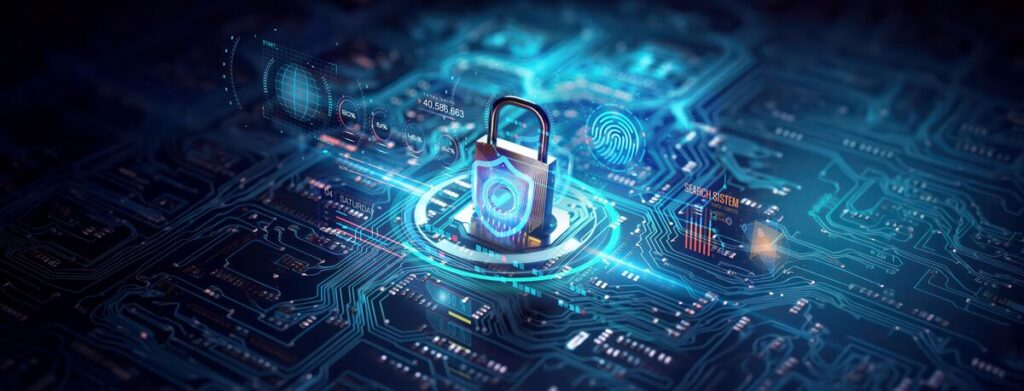
Businesses should also adopt proactive strategies, such as regular software updates and vulnerability assessments, to address emerging threats. Employee training on cybersecurity best practices further enhances protection, ensuring that systems remain secure.
Training and Adoption
Operators and technicians may require training to use new software effectively. Providing comprehensive training programs ensures a smooth transition and maximizes the software’s potential. Hands-on workshops and tutorials can help employees familiarize themselves with the new system.
Additionally, businesses should foster a culture of continuous learning. By encouraging employees to stay updated on the latest advancements, they can ensure that their workforce remains skilled and adaptable to technological changes.
By addressing these challenges with well-planned strategies, companies can ensure successful software integration and fully leverage its benefits.
Examples of Software-Integrated Control Panels
Software-integrated control panels are transforming how industries manage processes and optimize operations. These examples highlight the diverse applications of advanced software solutions in meeting industry-specific challenges and enhancing overall performance.
Automotive Industry
In the automotive sector, control panels with integrated software manage assembly lines, ensuring precision and consistency. For example, robotic arms are programmed to perform tasks such as welding and painting with minimal error. These systems rely on real-time data to adjust operations, maintaining high-quality standards.
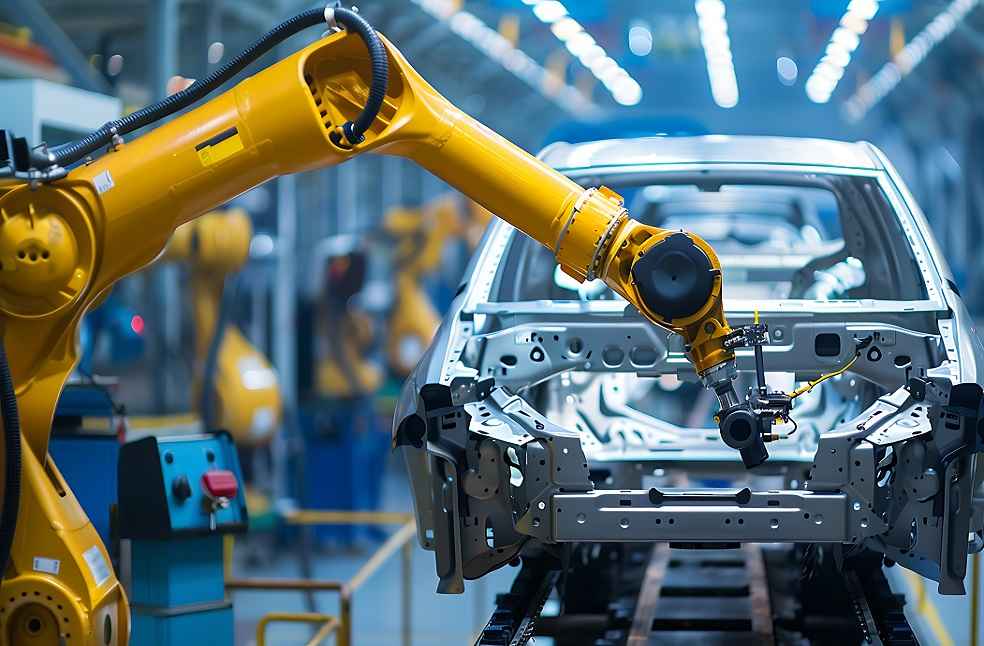
Software integration also supports innovation in vehicle manufacturing. From managing complex supply chains to optimizing production schedules, advanced control panels enable automakers to meet growing consumer demands efficiently.
Food and Beverage Processing
Control panels in this industry monitor variables like temperature, pressure, and humidity. Software integration ensures that these parameters remain within acceptable ranges, maintaining product quality and safety. Automated alerts notify operators when adjustments are needed, preventing potential issues.
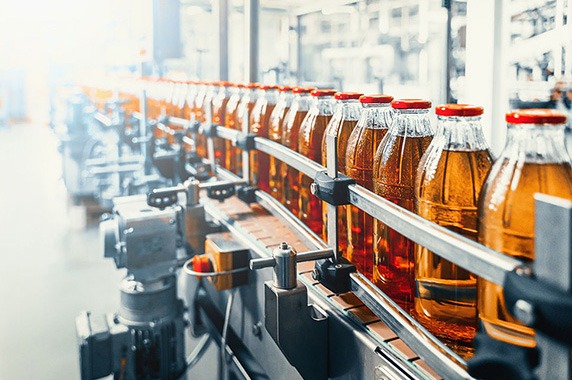
Additionally, integrated software facilitates compliance with regulatory standards. By maintaining detailed records of production processes, businesses can demonstrate adherence to safety guidelines, reducing the risk of penalties or recalls.
Energy and Utilities
Energy grids and utility systems rely on software-integrated control panels for efficient distribution and monitoring. Renewable energy plants, such as solar farms, use these systems to track performance and optimize output. Real-time monitoring ensures that energy generation aligns with demand, minimizing waste.
In addition to improving efficiency, software integration supports sustainability goals. By identifying opportunities for energy savings, control panels help businesses reduce their environmental impact while maintaining profitability.
These examples illustrate the versatility and effectiveness of software-integrated control panels across different industries. By tailoring solutions to specific operational needs, businesses can unlock significant value and ensure long-term success.
Conclusion
Integrating software into industrial control panel design is transforming the way industries operate. From real-time monitoring to enhanced automation, these advancements bring significant benefits. While challenges such as compatibility and cybersecurity remain, ongoing innovations continue to address these issues. By adopting the latest technologies, businesses can enhance efficiency, safety, and scalability. As software integration evolves, it will play an even greater role in shaping the future of industrial operations.
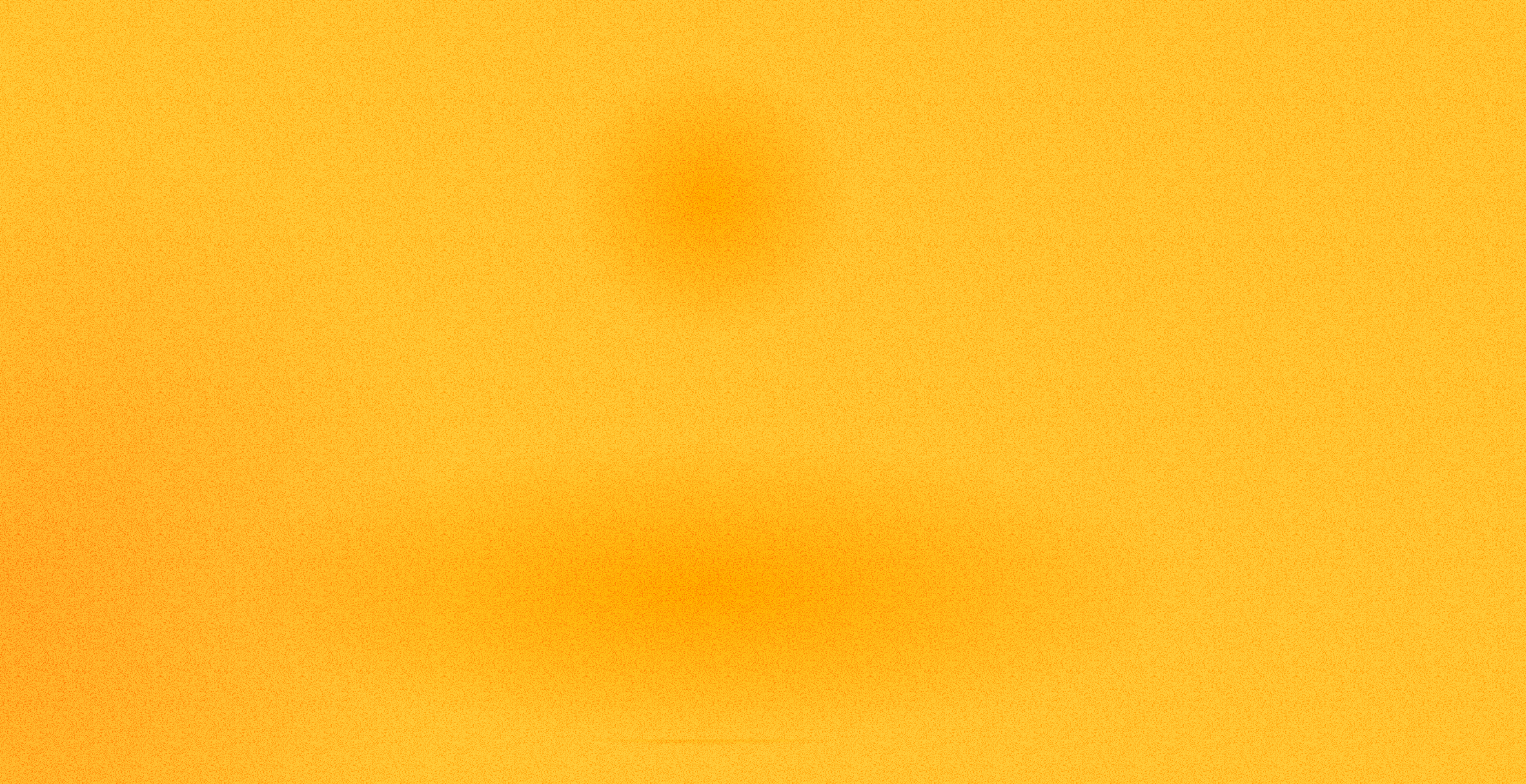
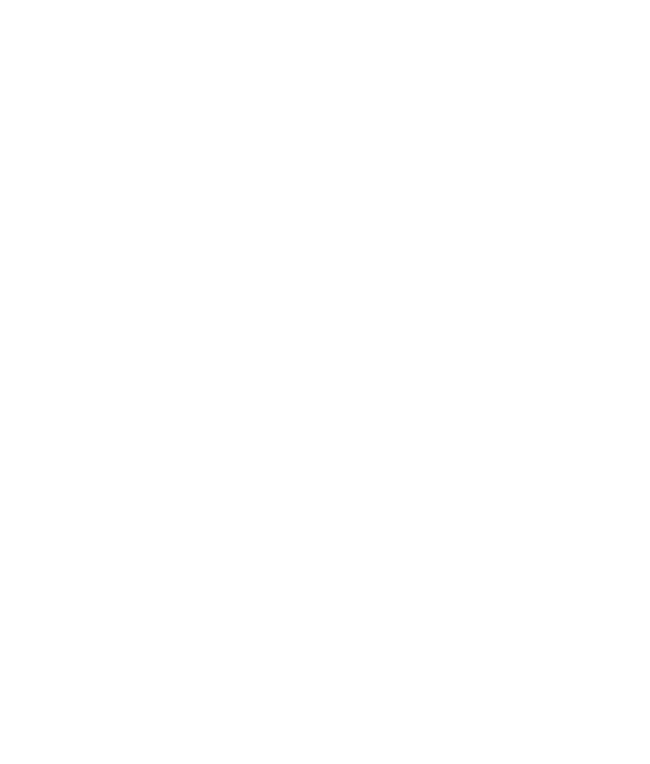
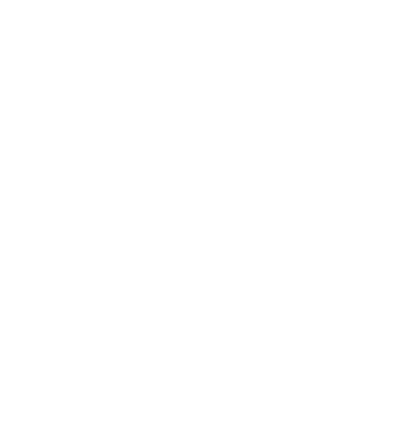
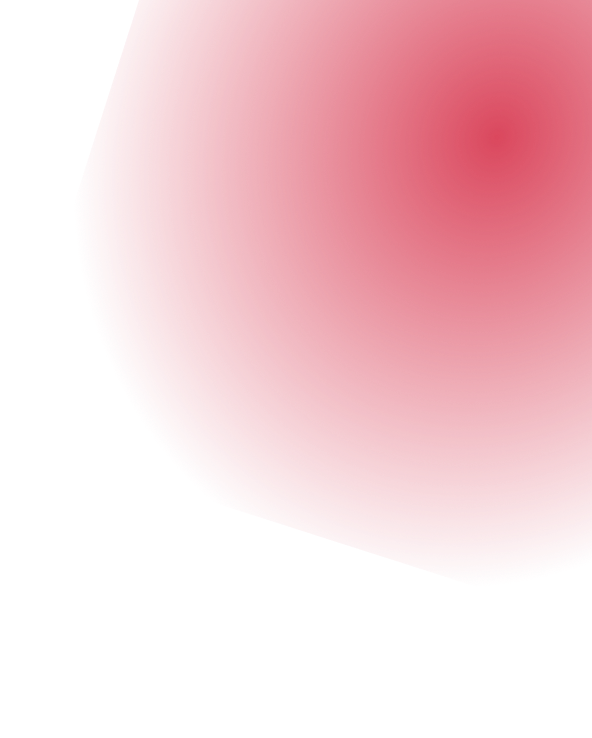
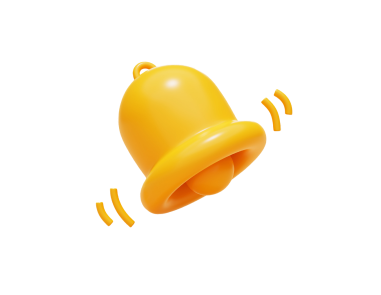
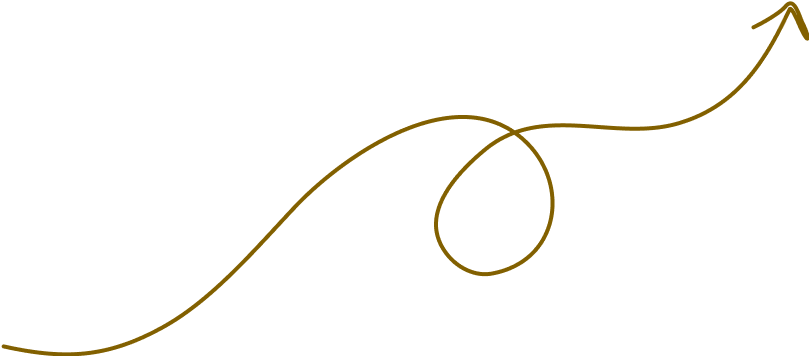
Read more topics
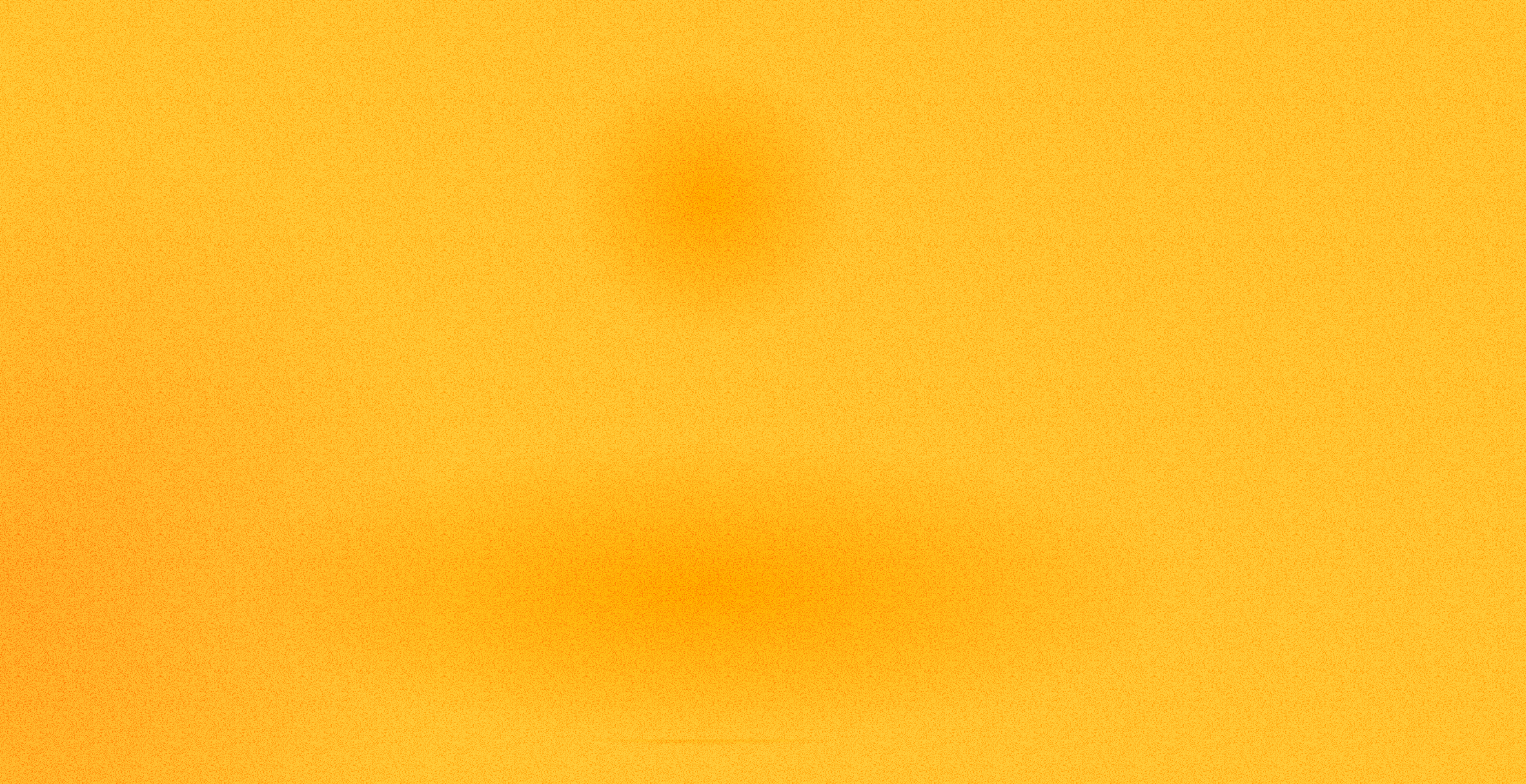
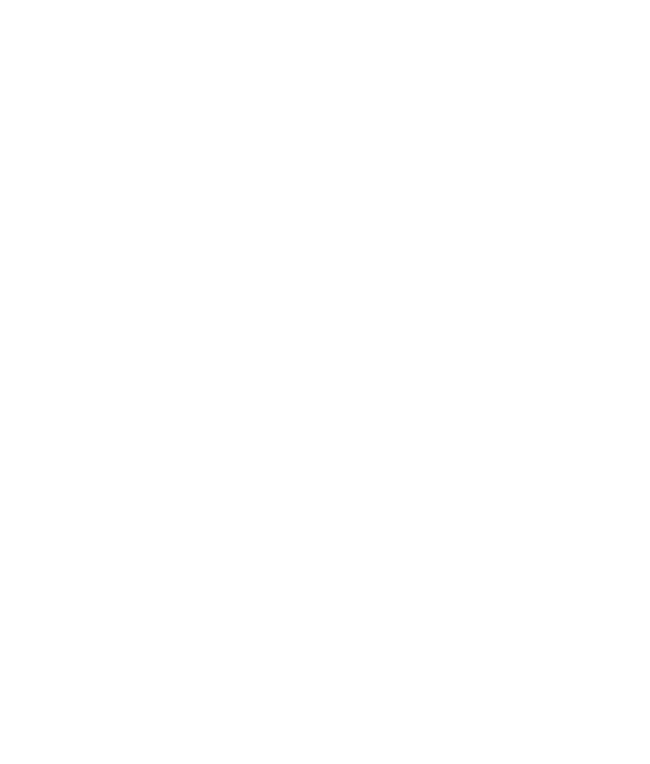
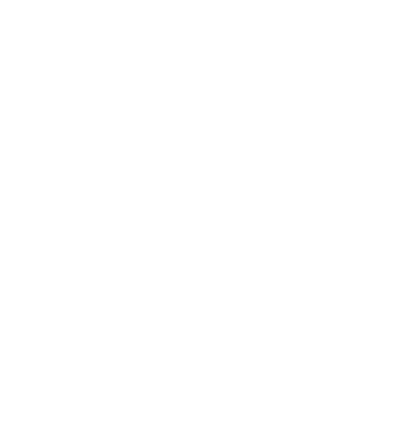
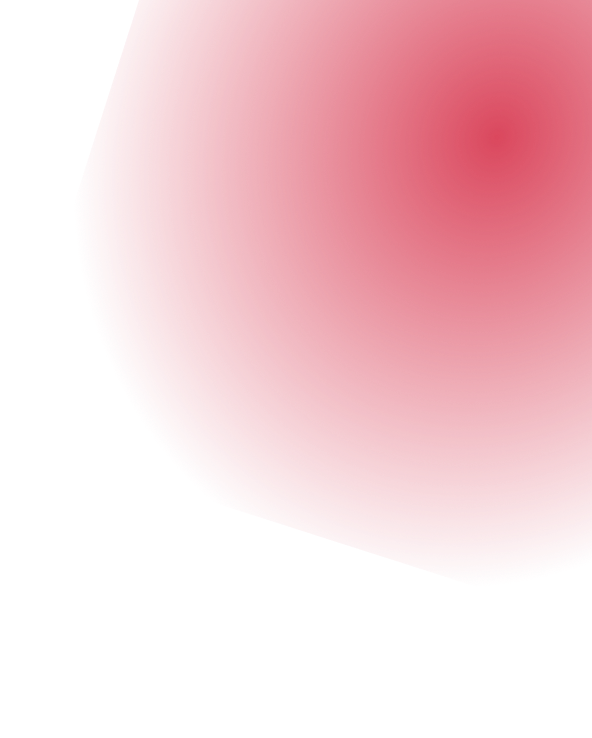
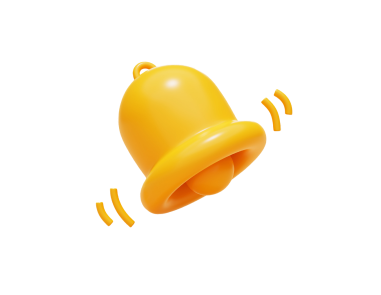
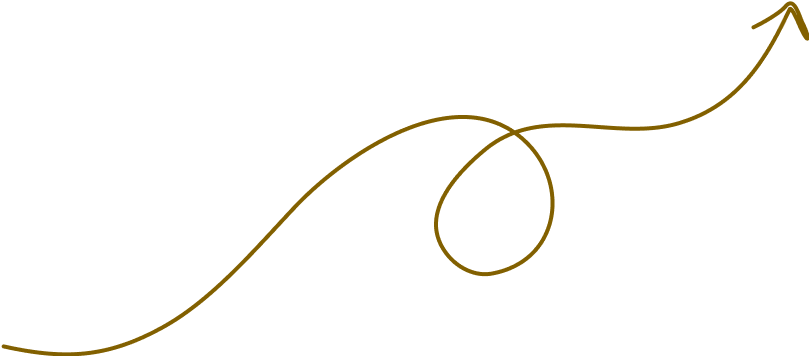